MEET OUR PEOPLE
Get to know the faces behind the company
From seasoned engineers and innovative designers to dedicated support staff and passionate apprentices, every member of AAG brings unique skills and perspectives that contribute to our success.
Get to know the faces behind the company, learn about their roles, and discover the passion and expertise that drive Atlantic Aviation Group to new heights.
Meet the people behind the maintenance in our video series below
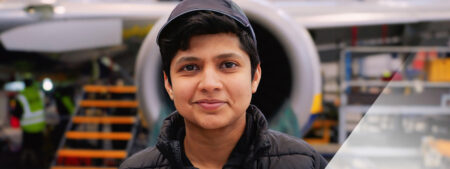
Prarthana Pardeshi »
Lead Engineer
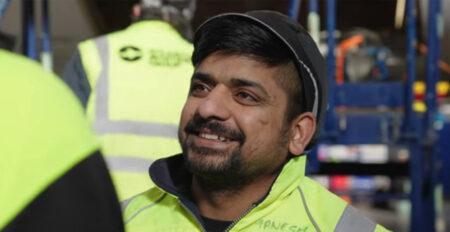
Ganesh Devkota »
Team Leader - Engines and Landing Gears
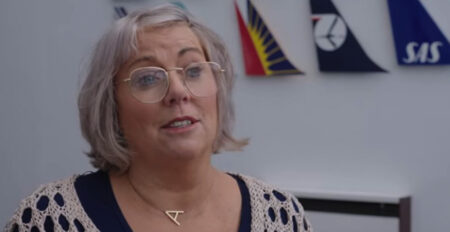
Anna Maria Barrett »
Commercial Buyer
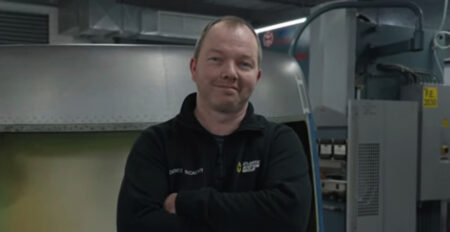
Dermot McCarthy »
Structures and Support Shops Lead
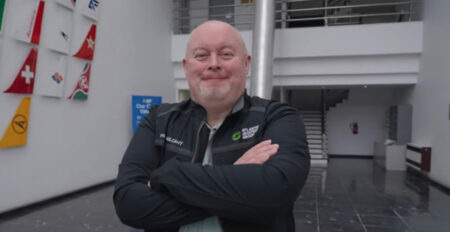
Paddy Mulcahy »
Planning Lead
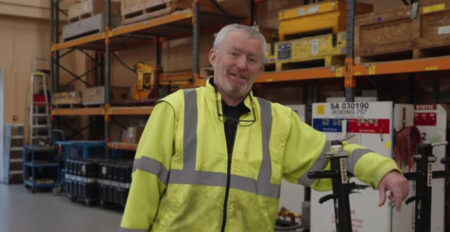
Paul O’Flanagan »
Toolcrib Team Leader
Start Your Career
Embark on an exciting journey with Atlantic Aviation Group, where your career can take flight.
Our training programmes are designed to equip you with the skills and knowledge needed to excel in the aviation industry. Choose from our award winning 4 Year Apprenticeship or 2 Year Traineeship.
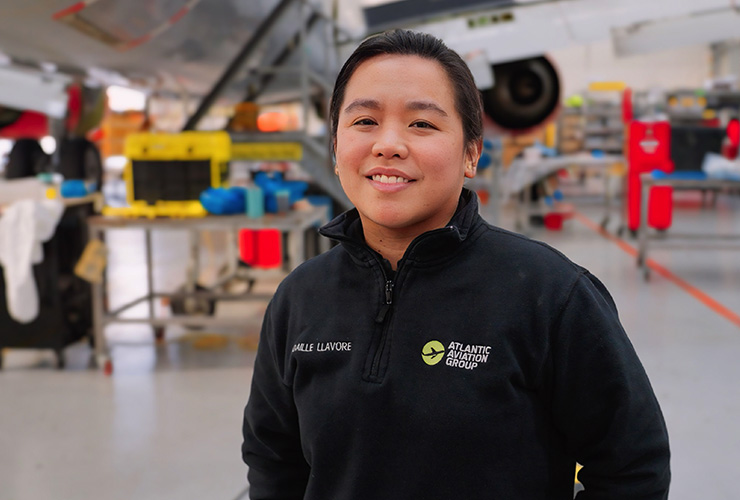